
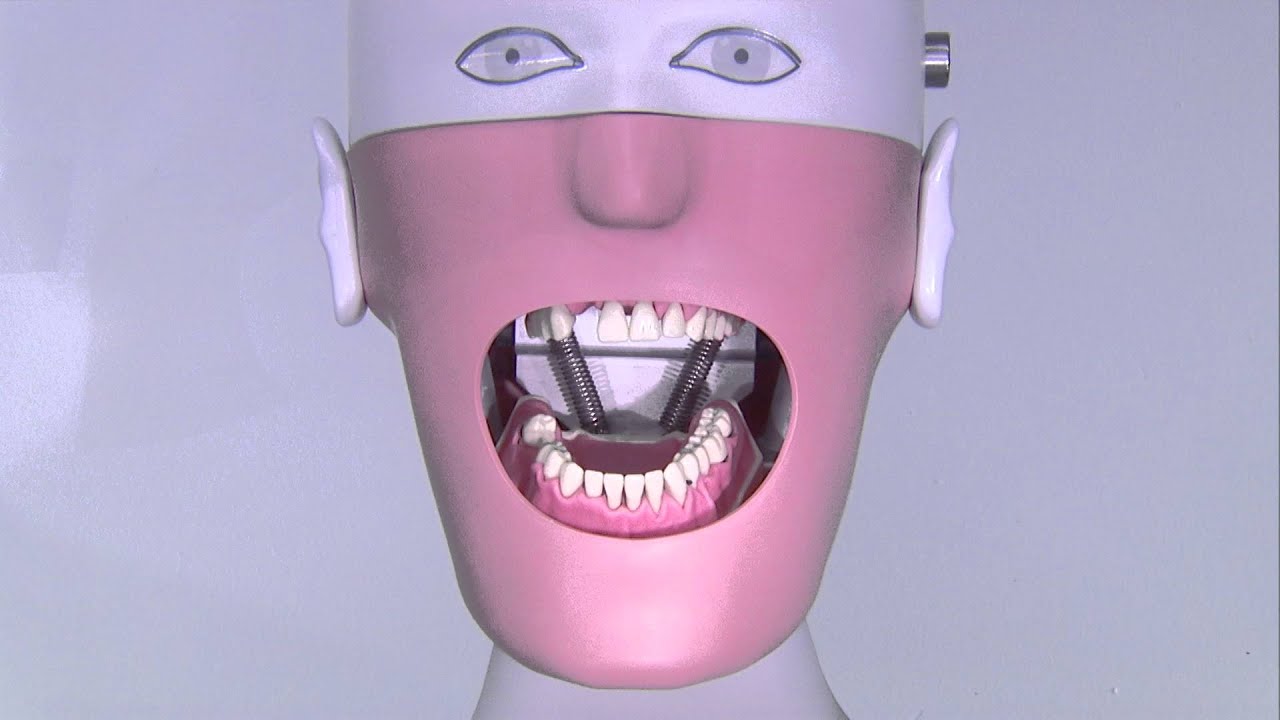
All adhesives contain a solvent, which evaporates leaving a film of adhesive which will then bond to the impression material. It is important that the correct type of tray adhesive should be used with its corresponding impression material. Most tray adhesives are specific to each generic group of impression materials ( Table 15.1). Application of adhesive to the tray thus becomes more difficult and the adhesive layer deposited is thicker than desired, leading to reduced performance.

This means that the seal on the lid becomes less secure with time, leading to evaporation of the solvent and the consequent thickening of the adhesive. Invariably, as the adhesive lasts for long periods of time, the excess adhesive from each application gets deposited around the neck of the bottle. Most tray adhesives are provided in screw-top bottles with a brush affixed to the lid ( Figure 15.10). None of the available adhesives is particularly effective and it is unwise to rely on adhesive alone in the tray. For the most effective use, two thin coats should be applied with the first coat being allowed to dry before the application of the second. Pooling of excess adhesive is undesirable as the solution will not dry and will weaken the bond between the impression material and the tray. The adhesive should be applied sparingly to the internal surface of the tray and extended just over the margin of the tray to the external surface to ensure that the periphery of the impression material remains attached to the tray. Failure to let the material dry will adversely affect the union between the tray, adhesive and impression material. This means that they should be applied to the tray and allowed to dry in advance of the impression being taken. Additional perforations will reduce this but not eliminate it completely.Īll tray adhesives are based on contact adhesive technology. (B) A perforated tray, where the impression material has pulled away from the tray wall between and despite the presence of perforations. 15.9 (A) A rim-lock tray, where the impression has pulled away from the tray as a result of the polymerization shrinkage. All of these impression materials require to be supported in an impression tray and be retained there until after casting.įig. This is called a total process chain.Īll the impression materials which are available to the dentist have various degrees of accuracy and the indication of the material will depend on the need for detail on the working cast. Therefore, an impression that is too accurate may not work as the inaccuracies in the other stages in the process are not taken into account. The inaccuracies at each stage must compensate for each other so that the final restoration will fit accurately. Inaccuracies can occur at any stage in the process of constructing any dental device. Compatible with all model construction materials.Remain dimensionally stable after removal.Easily removable from the mouth especially from undercut areas.
