
Reverse breakdown voltage is often a few hundred volts. The Diode, (more likely the diode trio) in your alternator is a lot tougher than any of the electronics are. When current starts trying to find its way through your machine trying to find a ground is when it gets bad. Now with a bad ground clamp connection, and a welding machine that has an earth ground, well, most anything is possibile then. The path of least resistance comes into play. Disconnecting the battery, and keeping the ground clamp nearby where the welding is done is about all you can do. I'd say your alternator went out on its own. Depending on where I'm welding and what machine I'm working on I would also disconnect the computer as well. Given the cost of a computer and all the rest of the components I would suggest at the very least disconnecting the battery. I have seen fry marks on engine crankshafts from just this practice. Putting the ground clamp on the track and welding on the bucket though will cause you grief and possibly not just to the computer. Going back to the computer issue I'm sure there is little chance of burning a computer when the welder ground is connected next to the place being welded. The rest of the manufacturers have somewhat less. The Komatsu product has between 16 and 20 diodes in the wiring harness to protect against voltage spikes. It's not necessarily something someone did to cause it. Alternators like all other man made components wear out. Some use a third wire as a signal that the engine is running while others use it as a frequency indicator which is calibrated to the speed of the engine. The diode problem in the alternators is something very common to almost all Japanese designed excavators. Off to test the Alternator now, hoping it's nothing else!!
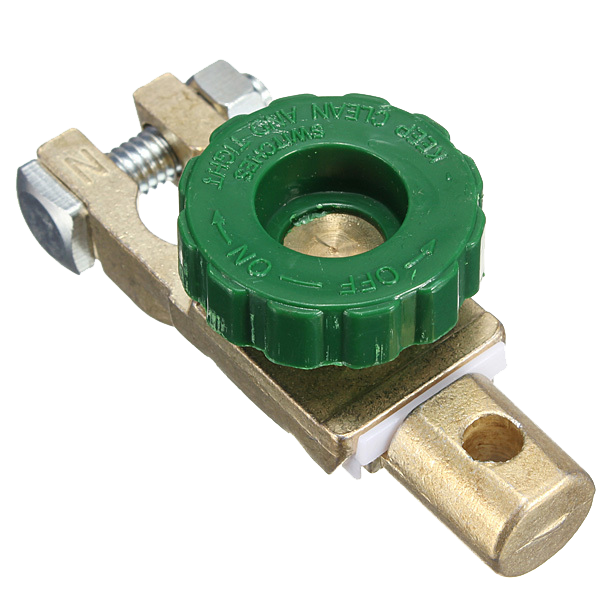
I think others should be aware of the dangers of welding machines (I certainly admit to thinking wrongly a battery disconnect was ok) and know of the correct manufacturer procedures to follow.
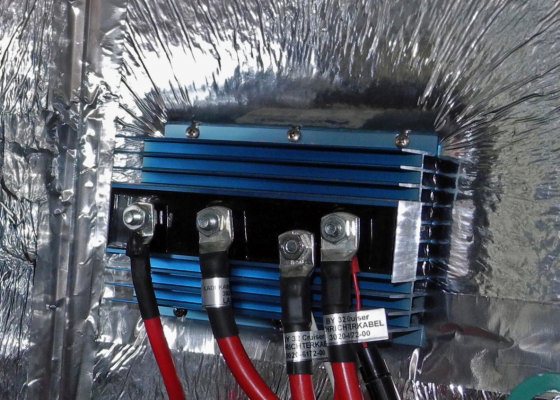
The machine has worked perfectly for 2 weeks now so should I get away with it, or is disaster looming? If confirmed the Alternator replacement or repair will be a valuable lesson, but if the computer fails a complete disaster. I have honestly never disconnected (or know anyone else who has) the computer on any CAT, Komatsu or JCB, but is the Hitachi different or particularily vulnerable. However I have since read a few horror stories of the damage done to the computers by welding and the sometimes delayed reaction times before they fail. I took the precaution of disconnecting the battery and the earth clamp was directly onto the bracket, always close to the weld. That would normally be just one of those things, but it comes 2 weeks after having a large bracket MIG welded to the face of the dipper arm. It appears (unconfirmed) that the fault will lie with the alternator diode. I have just posted a thread about an electrical fault on my Hitachi Zaxis.
